10:30 am - 12:00 pm CDT
A1: Static Pressure Optimization
Systems Optimization
Static Pressure Optimization: Best Practices Learned the Hard Way!
Part One
Static pressure provides a primary means for maintaining safety within the laboratory environment. It keeps the potentially noxious air within the lab from escaping into the rest of the building, it drives the ventilation effectiveness within the laboratory, and it provides the airflow requirements for exposure control devices to operate safely. The laboratory exhaust fans are primarily responsible for providing the negative air pressure that is necessary to safely operate the facility. However, these exhaust fans are also responsible for jetisoning any toxic and/or odorous material out of the lab without adversely exposing critical areas downwind of the exhaust stack.
These two roles can work in opposition of one another if proper static pressure control is not maintained. Often increasing duct static pressure is seen as a means for fixing poor design; leaky duct, increase the static pressure; fume hood in alarm, increase the static pressure; insufficient pressure gradient between spaces, increase the static pressure. In some cases, increasing the static pressure may inhibit the fans' ability to provide sufficent plume rise to make a safe environment downwind of the stack, but in every case it will increase the energy consumption of the exhaust fans. So, just increasing the static pressure should not be an end-all be-all for fixing air flow issues within the lab.
Static Pressure Optimization: Best Practices Learned the Hard Way!
Part Two
Optimizing laboratory exhaust duct static pressure had long been considered the “last mile” in lab ventilation energy savings. Historically, the energy savings from duct static optimization was all but eliminated by design strategies that decoupled the stack velocity and static pressure control by controlling static pressure with outside air bleeding directly into the plenum while running the exhaust fan at a constant stack velocity set to avoid re-entrainment for the worst-case conditions of cross-wind velocities and contaminant loading. Today, building codes recognize and require optimization of exhaust stack velocity based on dispersion modeling, in many cases eliminating the outside air bleed damper and making duct static pressure control one of the control variables to be considered in parallel with stack velocity. While this approach evaluates the risk of exposure to people outside the lab facility, the practice must also be bounded by impact on risk of exposure to the lab occupants.
While Part 1 focuses on stack velocity and the environment outside the lab building, this presentation focuses on the environment inside. It will discuss the parameters for lab airflow control devices and room conditions that drive the local requirement for duct static pressure and how these parameters are used in the sequence of operations to determine the exhaust fan pressure set point to achieve the optimal safe and sustainable operation. Case study examples will be presented.
Static Pressure Optimization: Best Practices Learned the Hard Way!
Part Three
Static pressure optimization, both from a design aspect as well as a control strategy within a variable air volume system, is a key component to reducing energy consumption, as well as optimizing long-term operation of modern commercial HVAC systems. This strategy is not a golden key approach, because it depends upon proper design, controls integration, TAB and Cx to work as intended with optimum results. This session will discuss the considerations related to TAB and Cx.
A2: Green Lab Leadership and Certification
Green Labs
AstraZeneca's Green Lab Journey
In 2020, AstraZeneca’s Green Lab Journey within the quality function began. The challenge was to prioritize sustainability on a level comparable to safety and health. The plan was to educate, empower, and deliver using the My Green Lab certification program. Two laboratories were chosen as pilots for the initiative. Both sites collaborated with My Green Lab (MGL) and began the certification process.
Green level certification was achieved by both pilot labs within a year of implementation following the MGL certification program guidelines. Over the next two years, integration of a sustainable culture continued throughout AstraZeneca’s quality laboratories using the MGL certification to empower scientist and deliver results. Each QC laboratory in the Americas region obtained green level certification status. The entire journey has been inspirational and rewarding due to the difficult challenge of implementing considerable change under such stringent requirements. The increased engagement has made associates aware of the importance of sustainability. The MGL certification process provided the tools to make sustainable changes. Data was collected and site leaders used the data to develop plans and drive performance. The next step of the ongoing quest to save the planet via the laboratory, is to continue maintaining a sustainable culture. One of the original pilot sites achieved this goal and became the first QC laboratory to obtain re-certification under the MGL program.
It Takes a Village: Revising the My Green Labs Certification Program for Greater Impact
My Green Lab Certification is recognized by the United Nations Race to Zero Breakthrough Outcomes campaign as a key measure of progress toward a zero-carbon future and is widely considered the Gold standard for laboratory sustainability best practices around the world. The certification program from My Green Lab provides lab personnel and supporting staff with actionable ways to make impactful changes by focusing on the behavioral and operational aspects of how labs work. The expansion and success of the program is demonstrated through over 2,000 labs becoming My Green Lab certified in recent years. Seeking continuous improvement, in 2023 and 2024, My Green Lab certification underwent a revision and update process with guidance from numerous industry and academic stakeholders. This presentation will focus on key changes that have been made to the My Green Lab Certification Program in the revision, and the scientific motivations for these changes. This presentation will also discuss third-party verification of certification programs and the European Union’s recent Green Claims Directive.
Go Big or Go Home: Building a Program Meant to Last
The UAB Green Labs Program started in 2016 with a unique approach to lab engagement. This approach helped the program grow five-fold within a few years and allowed UAB to justify further development of the program.
UAB Green Labs requires half of all lab members to take a My Green Lab survey and attend a presentation. This presentation reviews sustainable lab techniques specific to the lab. Labs provide deliverables such as chemical and purchasing inventories, equipment usage rates, and cold storage practices to maximize sustainable efforts. These deliverables are analyzed by the Green Labs Team, and sustainable alternatives and improvements are provided back to the lab. Two weeks after the presentation, a walkthrough of the lab is completed to help adopt additional sustainable initiatives that were discussed during the presentation.
These labs receive benefits that improve lab operations and foster a sustainable culture: free freezer maintenance, a boilerplate template for R-1 grant applications, and lab recycling are such benefits.
UAB Green Labs assists and verifies sustainable changes are made with minimal effort on the researchers' part while also providing incentives to being a green lab. This is beneficial since a barrier to program participation is often the perceived time commitment that labs must make to be sustainable. This process allows the program to provide assistance concurrently to maximize energy, water, and waste savings across a variety of different labs.
A3: Design for Carbon Reduction
Sustainable Design
A Certified Zero Energy Laboratory
Vertex has committed to reduce their emissions by 42 percent by 2032. The company strives to minimize fossil fuel consumption and evaluate options to rely on renewable energy at all its operations. This session presents the tangible implementation of these goals through the case study of the Leiden Center 1 building, a 280,000 square-foot laboratory building recently constructed in the Boston Seaport.
The Leiden Center 1 was recently awarded LEED Platinum. This session provides the attendees with tangible examples of how the owner and design team navigated these expectations, vetted specific solutions, worked through project challenges, and was ultimately successful. From high-efficiency systems to partial electrification of heating, and from advanced heat recovery to on- and off-site renewable energy, we illustrate the financial and logistical considerations that drove the final decisions.
Advancing Sustainable Practices in a World-Class Neuroscience Research Facility
The construction of the Neuroscience Research Building on the Washington University Medical Campus marks a significant stride towards environmentally conscious research infrastructure. With a focus on sustainability, the building integrates numerous features aimed at reducing its environmental impact while fostering groundbreaking neuroscience research. This building became the first lab building to be permitted under St. Louis’ latest code revision, which allowed for a broader user engagement conversation involving both the research and facility staff.
Through user engagement, both energy and carbon reductions occurred over the course of the design phases, resulting in a 41 percent reduction in EUI between schematic design and construction. Energy efficiency measures are used extensively from energy-efficient ULT freezers, heat recovery chillers, and LED lighting. Every aspect of the facility design prioritizes efficiency without compromising research needs. Additionally, initiatives such as low-flow water systems, noise reduction measures, and bird-strike prevention mechanisms underscore a holistic commitment to sustainability and occupant well-being. This presentation will delve into the innovative design strategies and collaborative efforts driving the attainment of LEED Gold certification and advancing sustainable practices in this state-of-the-art research facility.
Reducing Carbon Impacts in Lab Buildings
This session provides a case study on a holistic approach to analyzing and reducing carbon emissions in lab buildings. The fourth phase of Edwards Lifesciences’ campus, the Mussallem Innovation Center, celebrates the medical device maker’s culture of collaboration and innovation. Home to the company’s Centers of Excellence, the 118,600 square-foot, three-story lab and office building puts innovation on display and functions as a new nerve center for groundbreaking research and development on the campus.
The project team utilized a design approach that took a comprehensive look at reducing carbon emissions. Operational emissions were reduced through the use of passive architectural strategies and the optimization of active systems such as lighting and mechanical equipment. Resulting building loads were then further offset through the introduction of on-site renewable energy. Embodied carbon was reduced through the inclusion of mass timber and careful specification, limiting the emissions of building materials such as concrete. Analysis of the project site and the amount of emissions that could be sequestered through a thoughtful approach to the landscape design provided a comprehensive understanding of the project’s total carbon impact.
The case study will share the analysis and tools that were used by the project team to help inform the final constructed solution that is completing LEED Gold certification.
A4: Decarbonization Strategies and Standards
Decarbonization
Roadmap for High-Performance Zero Carbon Labs Based on a Life Cycle Approach
Labs are widely know to be a prodigious consumer of energy. Labs also have significant higher carbon footprint, higher water consumption and higher waste generation.
On a per square foot basis, labs can consume 5 to 10 times more energy than office buildings. Unlike office buildings, which are typically designed around a ventilation standard of 20 cubic feet per minute (cfm) per person of outside air equal to about one air change per hour (ACH) or less—lab modules normally require 100 percent outside air often at exchange rates between 6 and 12 ACH—to meet the aggressive exhaust requirements of fume hoods. Also, in comparison to other institutional and commercial buildings, laboratories may also have high plug loads that can dominate the energy pie, and from an energy efficiency perspective these can often being overlooked.
This presentation provides a holistic road map for designing a high-performance zero carbon lab based on a life cycle approach.
Breaking Barriers: A Strategic Blueprint for Lab Building Decarbonization
Numerous challenges hinder the process of decarbonizing laboratory buildings, including concerns related to safety, expenses, timelines, and the magnitude of the energy transition. During this presentation a case study from a leading pharmaceutical manufacturer will show the comparison between traditional airflow optimization project methodologies and a new approach essential for intricate retrofit projects within labs. This approach is necessary for an effective decarbonization initiative and should extend beyond the adoption of new technologies, incorporating inventive financing strategies, utilization of rebate incentives, and avoidance of carbon penalties, all while integrating cutting-edge technology to achieve optimal efficiency enhancements. The case study will review the process used during the project and results.
ASHRAE Standard 211 Updates and Impact to Lab Facilities
ASHRAE is re-constituting the Standard 211 for Energy Audits to make updates including how to address decarbonization assessments. The presentation will show some examples of how laboratory facilities may be affected by updates to the standard and demonstrate results of several assessments. Attendee Q&A may also identify specific concerns from the I2SL membership pertaining to ASHRAE Standard 211.
Thank you to our sponsors!
Platinum

Gold
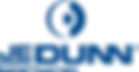
Silver
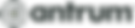

Bronze
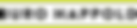
